Phoenix 3D Printing is a process of turning digital files into physical models, layer by layer. It is used to create objects from polymers, metals and ceramics.
Once a model is designed, software programs “slice” it into layers. This allows the printer to build a structure by directing the nozzle where to place each layer.
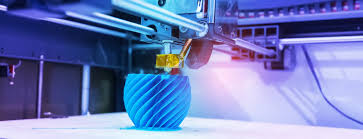
3D printing is a great way to create physical prototypes for product development and testing. It allows engineers to easily iterate on a design and quickly produce new prototypes that closely match the original design intent. This helps to improve quality and reduces costs by eliminating the need to make costly changes to a final design. The process of creating a prototype with 3D printers is also much faster than traditional manufacturing methods. This means that a company can go from concept to prototype in less time, which can dramatically improve their time-to-market.
There are a number of different ways to create a prototype, but the most common is using fused deposition modeling (FDM). This method uses a heated nozzle to extrude thermoplastic material layer by layer. The result is a high-quality prototype with a smooth finish. 3D printing is also highly versatile, allowing engineers to print almost any type of product, provided it fits within the printer’s build volume. The versatility of this method also makes it possible to customize products for specific markets or individual customers.
The design process for a new product begins with a concept, which is then translated into a digital model using computer-aided design software. This allows designers to examine the model for desired functionality, aesthetics, and manufacturability. The model is then converted into a standard file format, such as an STL file, which is understood by most 3D printers.
Once a prototype is created, it can be subjected to rigorous testing and user feedback to evaluate its performance and determine areas for improvement. This testing can identify design flaws and technical issues that may not be obvious during the conceptualization phase. It is also possible to create parallel prototypes with different functions in order to test each function independently.
The ability to iterate and refine a product’s design has numerous applications across industries. For example, aerospace engineering can benefit from rapid prototyping by enabling engineers to quickly and accurately test components. This has the potential to improve overall aircraft performance and efficiency by reducing weight and fuel consumption.
Cost-Effectiveness
3D printing opens new horizons for industrial product designers and engineers, enabling them to create intricate geometric designs. Without limitations on tooling and material stress parameters, they can experiment with geometries that would be impossible or prohibitively expensive using traditional manufacturing techniques. This freedom of design translates into lower costs. Moreover, the ability to print multiple iterations of a prototype allows for quicker and more cost-efficient design changes.
However, when evaluating the cost-effectiveness of an industrial 3D printer, it’s important to consider all the associated costs. These include labor, material and post processing expenses. In addition, different 3D printing technologies require varying raw material inputs. For example, some materials require a significant amount of post-processing to achieve a finished part. The good news is that these additional costs can be reduced by carefully planning your production.
Another major cost-saving benefit of industrial 3D printing is the reduction in waste. Traditional manufacturing processes produce a lot of excess material, which can add up to substantial costs. With additive manufacturing, only the exact amount of material is used to print a part or product, eliminating waste and saving money.
Industrial 3D printing has revolutionized the supply chain by allowing companies to manufacture parts directly on demand. This is a major shift in the way companies make products, as it eliminates the need for costly warehouses and cuts delivery costs. It also enables companies to create products locally, which helps them increase customer satisfaction.
The cost of composite materials for industrial 3D printing can be a barrier, but the technology offers great potential for cost-effectiveness. For example, carbon fiber and Kevlar strands can be printed to create structures with high strength-to-weight ratios. This is particularly useful for industries like aerospace and automotive, where weight-saving is paramount.
With all these benefits, it’s no wonder that many businesses are adopting this innovative technology to save time and money. This cost-effective technology is also transforming the world of education, with schools and universities using 3D printers to teach students how to turn CAD models into physical objects. It’s a great way to prepare the next generation of innovators for success.
Scalability
As 3D printing continues to evolve, scalability is becoming an important consideration. This technology offers the potential to transform manufacturing in a number of ways, including reducing supply chain costs and improving productivity. However, scalability can only be achieved by creating organized workflows and building efficient processes. These factors are crucial for a company to grow and remain profitable.
To achieve scalability, 3D printers should be used to produce multiple parts simultaneously. This will help reduce the time and cost associated with producing a single part, as well as the risk of errors that can occur during production. It will also enable the creation of complex components and improve the design and function of the product.
In addition to scalability, 3D printing can also improve operational efficiency. It can eliminate the need for assembly and other manual labor, thereby reducing the overall production cost. Additionally, it can create a more flexible and dynamic supply chain. This allows businesses to adopt just in time manufacturing strategies and reduce inventory levels.
As a result, companies can save money and increase profits. This is especially useful for smaller manufacturers that are struggling to compete with larger competitors. However, scalability is not possible without the proper software tools. It is vital to use a cloud-based 3D printing tool that can handle the needs of a large manufacturing business. The tool should include a customer-friendly front end, a backend workflow management system, and a library of models. It should also allow users to track customer communications in a logical way and keep the internal pipeline of work organized.
The scalability of additive manufacturing depends on a number of factors, such as the material used and the size of the print area. It also depends on the speed and complexity of the print job. For example, complex structures with smooth features can be fabricated at a rate above 10-3 mm3 s-1, which is comparable to that of conventional milling machines. However, these structures are still too large for most applications.
Customization
3D printing is revolutionizing the manufacturing industry by making customization possible on a large scale. This allows manufacturers to offer personalized products that meet the needs and preferences of consumers. However, achieving mass customization can be difficult without the right tools and processes in place. To ensure quality and consistency, it is important to integrate a fully digital workflow that includes design automation and optimized printing processes.
While the use of 3D printers has made inroads into consumer markets, many industrial users are still hesitant to adopt this technology. However, with its potential for rapid prototyping and cost-effective production, the technology is increasingly being used by product fabricators, healthcare experts, and construction engineers. This trend is expected to continue as the technology continues to improve.
Unlike traditional manufacturing methods, 3D printing eliminates the need for molds and assembly lines, which reduces lead times and costs. It also enables companies to produce complex parts in a shorter period of time. Moreover, it can be used to create multiple variants of the same part, allowing companies to better meet customers’ demands and increase sales. In addition to being more cost-effective, this process can help to reduce product defects and waste.
One of the biggest advantages of using a 3D printer is its ability to print complex geometries that would be impossible or impractical to produce with other techniques. This freedom of design allows manufacturers to tailor products to specific market segments and customer preferences, which can boost brand loyalty and sales.
Aside from its versatility, 3D printing can be used to fabricate a wide variety of materials. This makes it an ideal tool for creating prototypes, reducing design iterations, and testing new designs. It can also be used to make functional or aesthetic components for existing products. For example, Ford has partnered with 3D printing companies to enable customers to customize their vehicles with accessories that are functional, comfortable, and light. Peugeot is another manufacturer that offers a similar vehicle customization service with its FITS system, which provides storage space for various accessories.
Despite their simple appearance, 3D printers are sophisticated machines that require advanced software to operate. These programs manage the entire printing process, from the initial design to the final printed result. In addition to providing visual simulations of the printing process, these programs can also identify errors and help users improve their workflow. Additionally, they can help users determine the best material to use for their projects.